Proven Strategies to Enhance Efficiency in Manufacturing Operations
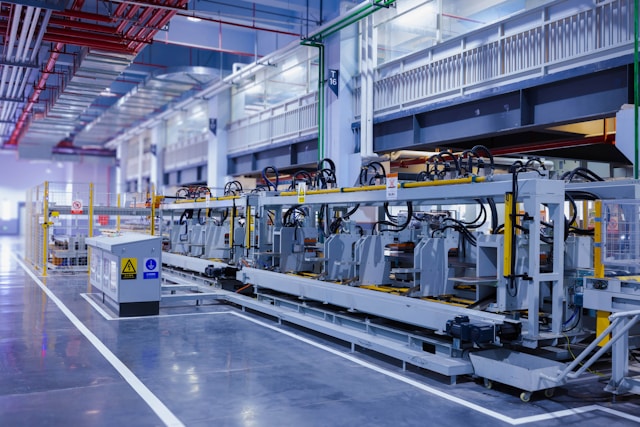
Achieving peak efficiency in manufacturing operations is essential for maintaining competitiveness and securing long-term growth. Manufacturers can significantly boost productivity and cut costs by streamlining methodologies, reducing waste, and adopting innovative technologies.
Effective strategies include optimizing workflows, enhancing employee training, and implementing automation. McKinsey estimates that recovering the historical pace of productivity development would add $10 trillion to the US GDP. These steps not only improve output but also help businesses adjust to evolving market demands.
In this article, we will discuss key methods to improve your manufacturing efficiency.
1. Implement Lean Manufacturing Principles
Lean manufacturing directions focus on eradicating waste, optimizing procedures, and maximizing value for the customer. It includes identifying value from the customer’s perspective, mapping out the value stream to pinpoint inefficiencies, and creating a smooth workflow by eliminating bottlenecks. By fostering a culture of constant improvement, manufacturers can respond to varying demands more effectively.
According to Industry Week, expanding lean manufacturing by 2-3 times could lay a sturdy foundation for the US economy recovery. The US economy could be a world leader again. Lean manufacturing has still not been employed by many US firms.
Incorporating lean principles reduces production costs, improves product quality, and shortens lead times, helping manufacturers enhance competitiveness. Additionally, lean practices promote employee engagement by empowering teams to take ownership of improvements, resulting in a more efficient, agile, and customer-focused manufacturing process.
What challenges might a manufacturer face when transitioning to lean practices?
Manufacturers transitioning to lean practices may need more support to change from employees, as lean often requires shifts in workflow and company culture. Additionally, implementing lean principles can be costly upfront, requiring investment in training and process redesign, which may temporarily disrupt production.
2. Invest in Staff Training and Development
Investing in employee learning and development is essential for improving manufacturing efficiency and maintaining a competitive edge. Well-trained workers are better equipped to operate machines, solve problems, and implement new technologies, reducing errors and downtime. Continuous development programs enhance workers’ skill sets, enabling them to adapt to developing industry needs and lean practices.
Ultimately, companies that prioritize training and development create a more skilled, agile, and motivated workforce, driving long-term success in manufacturing operations.
What is the return on investment (ROI) for employee training in manufacturing?
The ROI for employee training in manufacturing can be significant, often leading to increased productivity, reduced error rates, and lower operational costs. Studies have shown that businesses can see an ROI of up to 200% or more with well-trained employees. Additionally, investing in training enhances employee retention and satisfaction.
3. Utilize Advanced Technology and Automation
Utilizing advanced technology and automation is a pivotal strategy for enhancing efficiency in manufacturing operations. Technologies such as robotics, AI, and the Internet of Things (IoT) streamline production processes, reduce human mistakes, and enhance precision. Automation can take over repetitive tasks, allowing employees to focus on higher-value activities that require critical thinking and creativity.
According to Statista, businesses spent $2.15 trillion in 2023 for digital transformation in 2023. This expenditure is expected to reach $3.9 trillion by 2027. This investment not only promotes productivity but also increases employee engagement and retention by fostering a culture of digitalization.
Furthermore, advanced analytics can provide insights into operational performance, enabling manufacturers to identify areas for improvement and optimize resource allocation. By integrating these technologies, manufacturers can increase production speed, improve product quality, and remain agile in a competitive marketplace, ultimately driving growth and profitability.
What are the potential downsides of increased automation in manufacturing?
Increased automation in manufacturing can lead to potential downsides, such as job displacement, as machines and robots may replace human workers in certain tasks. Additionally, the initial investment costs for advanced technology can be high, which might strain financial resources, especially for smaller manufacturers.
4. Incorporate Laser Processing Solutions
Incorporating laser processing solutions into manufacturing operations offers numerous advantages that enhance precision, efficiency, and versatility. According to Novanta Photonics, more companies are adopting laser technology due to various advantages.
Laser technology enables precise cutting, engraving, and welding of materials with minimal thermal distortion, resulting in high-quality finished products. This adaptability allows manufacturers to work with a variety of materials, including metals, plastics, and fabrics, making it ideal for diverse applications.
Moreover, laser processing solutions can significantly reduce waste and operational costs by optimizing material usage and minimizing the need for secondary processing. By adopting laser solutions, manufacturers can improve production speed and flexibility while meeting the demands of an increasingly competitive market.
5. Optimize Supply Chain Management
Optimizing supply chain management is essential for enhancing manufacturing efficiency and ensuring the punctual delivery of products. By simplifying processes such as procurement, inventory management, and logistics, manufacturers can lessen lead times, lower expenses, and improve response to market demands.
Leveraging technologies like evolved analytics and real-time tracking allows businesses to gain better visibility into their supply chain, promoting proactive decision-making and risk management. Additionally, fostering strong connections with suppliers and implementing coordinated planning can lead to more reliable partnerships and improved communication.
According to Zippia, only 6% of companies are fully aware of their supply chain management. As many as 69% of firms do not have a complete insight into their supply chain. These figures need to improve. This is because an optimized supply chain not only improves operational efficacy but also contributes to higher consumer satisfaction and business expansion.
6. Monitor and Analyze Performance Metrics
Monitoring and analyzing performance metrics is essential for identifying areas of advancement and driving operational efficiency in manufacturing. By stalking key performance indicators (KPIs) such as production output, cycle time, and defect rates, manufacturers can gain practical insights into their processes. Utilizing cutting-edge analytics tools enables real-time monitoring, permitting for quick identification of bottlenecks or inefficiencies.
This proactive approach facilitates timely interventions, ultimately enhancing productivity and quality. Additionally, regular performance analysis fosters a culture of constant improvement. It also empowers teams to refine processes, set achievable goals, and adapt to changing market conditions, which contributes to long-term success in manufacturing operations.
Embracing Efficiency for Sustainable Growth
Enhancing efficiency in manufacturing operations is essential for remaining competitive in today’s dynamic market. By implementing strategies such as lean principles and investing in employee development, manufacturers can drive productivity, reduce costs, and ultimately achieve sustainable growth. Continuous monitoring, utilizing advanced technologies, and optimizing supply chain management are key to long-term success.