Master the Cut: Superior Metal Cutting Tools for Industry Experts
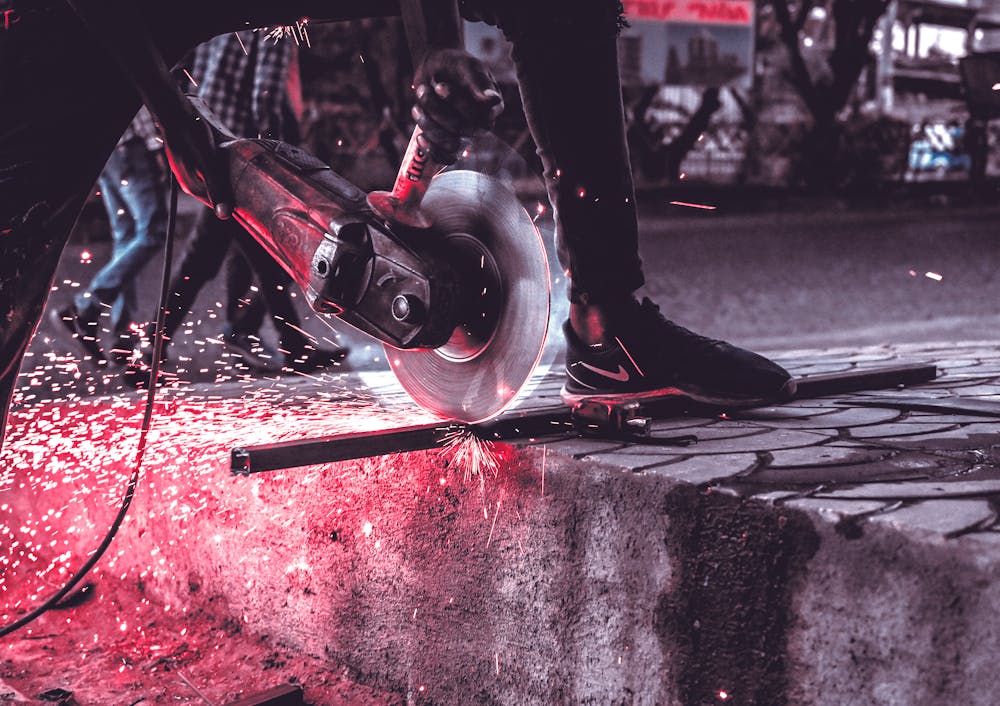
Precision in metal cutting is of the utmost importance in industries such as aerospace, automotive, and manufacturing. Achieving the highest level of accuracy ensures the quality of the final product and the efficiency and safety of the production process.
Over the years, advancements in technology have revolutionised metal-cutting tools, introducing more efficient, precise, and versatile options.
This blog aims to highlight some of the superior metal-cutting tools available for industry experts. We also focus on the latest trends and innovations.
The Importance of Precision in Metal Cutting
Precision in metal cutting is critical for several reasons. First, it directly affects the quality of the finished product. In industries like aerospace, even the slightest deviation can lead to significant problems, including safety hazards. Precise cutting ensures that parts fit perfectly, function as intended and meet stringent industry standards.
Secondly, precision enhances efficiency. Accurate cuts reduce waste and rework, saving time and materials. This efficiency leads to cost savings and increased productivity, which are crucial for maintaining a competitive edge in any industry.
Lastly, precision impacts safety. Poorly cut metal parts can pose risks during assembly and use, potentially leading to accidents and injuries. High precision in metal cutting minimizes these risks, ensuring safer operations and products.
Trending Metal Cutting Tools
Recent advancements in metal-cutting technology have introduced several effective tools that offer superior precision and versatility. Here are some of the trending metal-cutting tools in the industry:
Plasma Cutters
Plasma-cutting technology utilizes electrically conductive gas to transfer energy from a power supply to any conductive material. As a result, it ensures a cleaner and faster cutting process. They are highly valued for their speed, precision, and versatility.
These plasma cutters can also cut through various metals, including steel, aluminum, and copper. They are used in automotive repair, industrial construction, and metal fabrication. Their ability to easily cut through thick and thin metals makes them indispensable in many fields.
Waterjet Cutters
Waterjet cutting technology uses a high-pressure stream of water, often mixed with an abrasive substance, to cut through materials. One primary benefit is that it does not produce heat-affected zones, which means it can cut materials without altering their properties.
They are capable of cutting a wide range of materials, including metal, stone, glass, and composites. This versatility makes them ideal for industries such as aerospace, automotive, and construction.
Top-rated waterjet cutting machines are praised for their precision, reliability, and ability to handle complex cutting tasks.
Laser Cutters
Laser-cutting technology employs a focused beam of light to cut materials. Its high precision makes it suitable for intricate designs and detailed work. Lasers are particularly effective for cutting thin metals and are widely used in industries that require high accuracy.
Beyond precision, laser cutting offers several compelling advantages. Due to the laser’s focused nature, it generates minimal material waste, optimizing resource efficiency.
Moreover, the high-speed operation of laser-cutting systems significantly enhances production rates. These factors collectively contribute to substantial cost-effectiveness, making laser cutting a financially attractive option for many businesses.
Common applications for this technology span across diverse sectors:
- electronics manufacturing
- Jewelry making,
- The medical device industry, and more.
CNC Milling Machines
CNC (Computer Numerical Control) milling machines are automated cutting tools that use computer programming to control their movements. This automation ensures consistent precision and allows for complex and repeatable operations.
CNC milling machines are advantageous due to their high level of accuracy, ability to handle complex shapes, and efficiency in mass production. They are commonly used in aerospace, automotive, and electronics manufacturing.
Additionally, their ability to produce parts with high dimensional accuracy often eliminates the need for subsequent finishing processes, further optimizing overall efficiency and profitability.
Choosing the Right Tool for Your Needs
Selecting the right metal cutting tool depends on several factors:
- Material Type: Different tools are better suited for different materials. So, you should choose the one that best suits your metal-cutting needs.
- Project Requirements: Consider the precision, speed, and complexity of the cuts needed. For example, laser cutters are ideal for intricate designs, whereas CNC milling machines are best for complex, repetitive tasks.
- Budget: High-quality tools come with varying price tags. It’s essential to balance the cost with the tool’s capabilities and the value it brings to your projects.
To maintain and optimize the performance of metal cutting tools, regular maintenance, proper usage, and staying updated with the latest technology are crucial.
Final Words
Precision metal cutting is the cornerstone of countless industries. Selecting the right tool for the job is paramount. Consider factors such as material, desired outcome, and safety. Regular maintenance ensures optimal performance. By mastering these tools and prioritizing safety, you’ll elevate your projects and achieve exceptional results.