Best Practices for Achieving Optimal Weld Outcomes in Production Welding
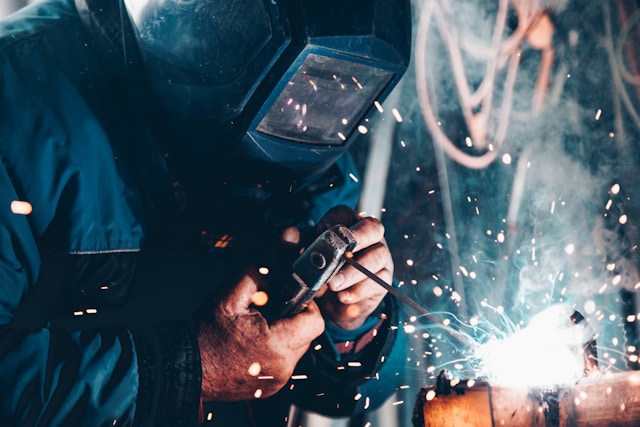
Professional welding is a critical process in production lines, integral to creating components that meet rigorous quality and performance standards. The effectiveness of welding directly impacts the overall functionality of the finished products. Expert welding helps maintain reliability and performance across diverse applications throughout the welding process, which is essential for achieving the desired weld outcomes and maintaining high standards in manufacturing.
Adopting Project-Specific Welding Solutions
Tailoring the welding process to address the unique requirements of each project helps optimize weld characteristics to enhance precision, efficiency, quality, and cost-effectiveness. Custom Production Welding solutions help meet specific needs by selecting the appropriate welding process, such as TIG, laser beam Welding, or Microscopic welding, based on material properties, joint design, and production requirements.
For instance, TIG welding might be ideal for its precision on thicker materials, while laser keyhole mode welding could be ideal for higher speed and efficiency on thicker sections. Expert welders precisely adjust parameters like heat input, filler materials, and joint configurations to ensure the welds achieve the desired strength and performance. The targeted approach contributes significantly to achieving the best possible weld outcomes, aligning with project goals and quality standards.
Optimizing Weld Characteristics
Ensuring welds meet specific performance criteria is crucial for achieving high-quality, reliable results. For instance, robust and durable welds like GTAW help joints endure operational stresses over time, such as those used in structural components or heavy machinery. Also, clean welds are critical for products where visual quality is paramount, like in consumer electronics or decorative items, necessitating laser welding for smooth, defect-free welds.
In precision machining, dimensional accuracy is non-negotiable, as it prevents distortion and maintains precise part dimensions, which is essential for airplane parts or automotive applications. Also, some welds must be corrosion-resistant to withstand acidic or salty environments. Considering fatigue resistance is vital for components subjected to cyclic loading, such as those in machinery or bridges.
Achieving these characteristics requires an experienced company with technical knowledge, skilled welding techniques, material science expertise, and rigorous quality control. This approach enables manufacturers and industry experts to significantly enhance product quality, reduce defects, and improve overall performance.
Effective Heat Management: A Cornerstone of Welding Success
Proper control of heat input minimizes issues like distortion, warping, and material damage, ensuring high-quality welds that maintain the desired properties of base materials. For example, precise control is achievable through amperage, arc length, and welding speed adjustments in TIG welding. The technique’s focused heat source helps to minimize the heat-affected zone (HAZ), preserving material integrity and reducing distortion. For larger projects, coolant use can further manage heat and prevent warping.
Due to the small scale of welds, microscopic TIG welding demands even greater heat precision. Specialized equipment and integrated cooling systems are essential for managing heat effectively, ensuring the integrity of tiny components. The precise focus of the laser beam and rapid cooling techniques, such as water or gas cooling, help manage heat and maintain weld quality.
Experienced welders adopt p[ractical strategies by selecting appropriate welding parameters, designing joints to minimize distortion, using proper fixturing, and employing cooling techniques. Such welding expertise can significantly enhance weld quality, reduce defects, and improve product performance.
Adherence to Industry Standards
Adherence to industry standards is essential in production welding, providing a foundation for quality, consistency, and safety in welding processes. Compliance with standards such as ISO 13485 for medical devices or AWS D17.2 for aerospace ensures that welds meet specific industry requirements and contribute to reliable outcomes.
Following these standards enhances product quality by ensuring welds achieve the necessary strength, durability, and appearance, leading to superior products. It also helps reduce defects and inconsistencies, minimizing the cost of production. Moreover, meeting industry standards ensures the use of safe inputs and materials, which is crucial for the safety of stakeholders in diverse applications of such welded components, creating safer environments.
Adherence to recognized standards facilitates international trade by demonstrating that products meet global quality and safety requirements. Outsourcing your welding needs to welders committed to these standards allows manufacturers to improve their competitiveness and reputation while ensuring high-quality, safe, and consistent welding outcomes.
A Focus on Accuracy and Consistency
Precise welds are fundamental to maintaining product performance and integrity, preventing defects, and reducing production costs. In safety-critical applications like aviation and medical equipment and tools, consistency ensures structural integrity, minimizing the risk of failures or accidents. It also helps reduce the need for post-welding rework and scrap.
Identifying professional welders like Micro Weld who have invested in well-maintained and calibrated equipment reduces the likelihood of equipment failures and inconsistencies, thus reducing downtime and increasing productivity. That helps manufacturers improve product quality, increase customer satisfaction, and drive business success.
In conclusion, strategically outsourcing your welding needs is essential to optimizing modern welding techniques, and ensuring precise product alignment with accuracy, safety, and reliability. Leveraging advanced welding technologies can significantly enhance your production capabilities. However, identifying an experienced welder like Micro Weld is the pivot towards achieving your final products’ highest quality and performance standards.